The Science Behind Porosity: A Comprehensive Guide for Welders and Fabricators
Comprehending the complex systems behind porosity in welding is vital for welders and makers pursuing impeccable craftsmanship. As metalworkers look into the midsts of this sensation, they reveal a globe regulated by numerous variables that influence the formation of these minuscule voids within welds. From the composition of the base materials to the intricacies of the welding procedure itself, a multitude of variables conspire to either intensify or ease the existence of porosity. In this extensive overview, we will decipher the science behind porosity, exploring its effects on weld high quality and unveiling advanced techniques for its control. Join us on this trip with the microcosm of welding imperfections, where accuracy fulfills understanding in the quest of flawless welds.
Understanding Porosity in Welding
FIRST SENTENCE:
Exam of porosity in welding exposes crucial insights right into the stability and top quality of the weld joint. Porosity, defined by the visibility of cavities or gaps within the weld steel, is a common problem in welding processes. These spaces, otherwise properly dealt with, can compromise the structural stability and mechanical residential properties of the weld, leading to prospective failures in the completed product.
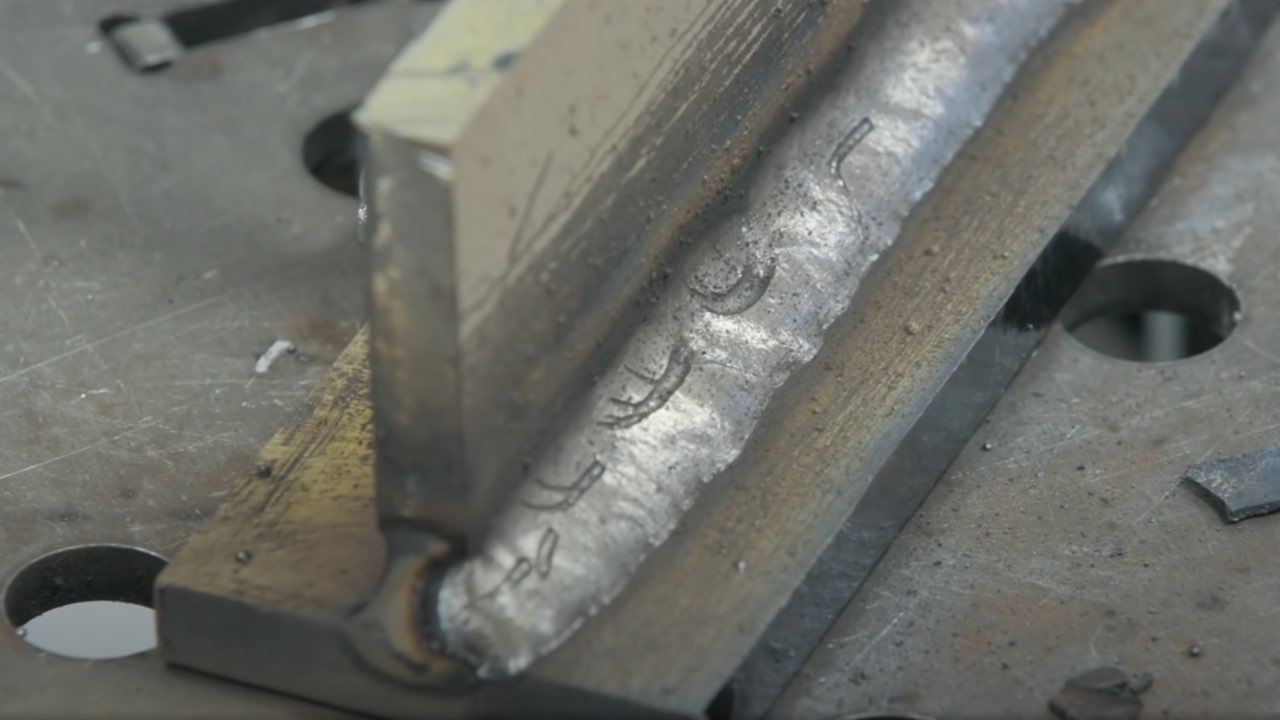
To identify and quantify porosity, non-destructive testing methods such as ultrasonic testing or X-ray inspection are frequently employed. These techniques permit the recognition of inner issues without compromising the honesty of the weld. By examining the size, form, and circulation of porosity within a weld, welders can make informed choices to enhance their welding procedures and attain sounder weld joints.
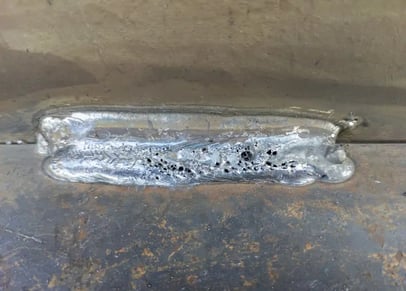
Aspects Influencing Porosity Development
The occurrence of porosity in welding is influenced by a myriad of variables, varying from gas shielding performance to the intricacies of welding criterion setups. Welding parameters, including voltage, present, travel rate, and electrode kind, additionally influence porosity development. The welding technique utilized, such as gas metal arc welding (GMAW) or secured metal arc welding (SMAW), can influence porosity formation due to variations in warm distribution and gas protection - What is Porosity.
Effects of Porosity on Weld High Quality
Porosity development dramatically endangers the structural honesty and mechanical residential or commercial properties of bonded joints. When porosity is present in a Web Site weld, it check these guys out creates voids or dental caries within the material, minimizing the general toughness of the joint. These voids act as stress and anxiety concentration factors, making the weld a lot more vulnerable to cracking and failure under lots. The visibility of porosity also compromises the weld's resistance to corrosion, as the caught air or gases within the gaps can react with the surrounding setting, causing deterioration with time. In addition, porosity can hinder the weld's capacity to hold up against stress or effect, additional endangering the overall quality and integrity of the welded framework. In crucial applications such as aerospace, auto, or structural constructions, where safety and security and sturdiness are vital, the damaging results of porosity on weld high quality can have severe consequences, highlighting the importance of lessening porosity with correct welding techniques and procedures.
Methods to Decrease Porosity
Additionally, using the suitable welding parameters, such as the proper voltage, present, and take a trip rate, is essential in preventing porosity. Maintaining a regular arc size and angle throughout welding likewise aids decrease the probability of porosity.

Furthermore, choosing the best protecting have a peek at these guys gas and keeping correct gas circulation rates are crucial in lessening porosity. Utilizing the proper welding technique, such as back-stepping or employing a weaving motion, can likewise aid disperse warmth equally and minimize the chances of porosity development. Finally, making certain appropriate ventilation in the welding environment to remove any type of potential sources of contamination is vital for accomplishing porosity-free welds. By executing these techniques, welders can effectively lessen porosity and generate top notch bonded joints.
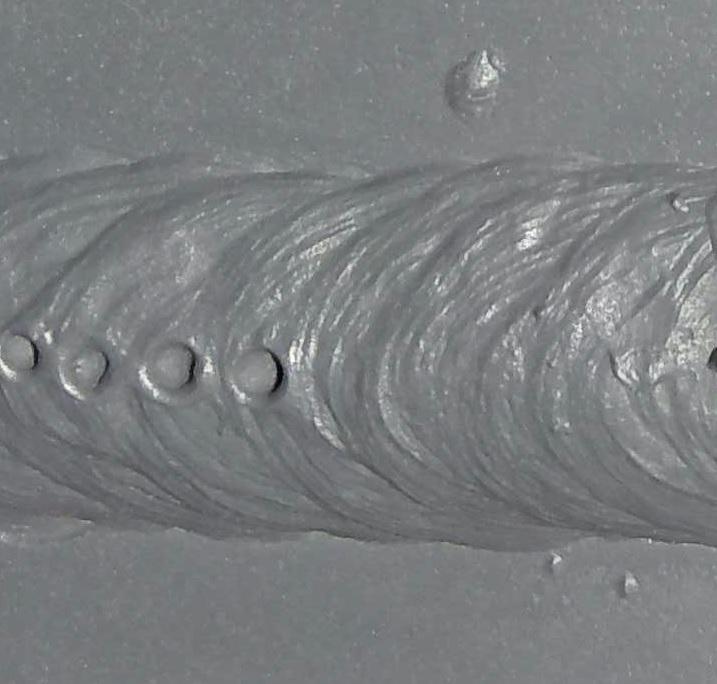
Advanced Solutions for Porosity Control
Carrying out advanced modern technologies and cutting-edge methods plays a critical role in achieving superior control over porosity in welding procedures. Furthermore, utilizing sophisticated welding methods such as pulsed MIG welding or customized atmosphere welding can also aid reduce porosity concerns.
Another innovative remedy includes making use of sophisticated welding tools. Making use of tools with integrated features like waveform control and innovative power resources can enhance weld quality and minimize porosity dangers. The execution of automated welding systems with exact control over criteria can substantially lessen porosity issues.
Furthermore, incorporating advanced monitoring and assessment modern technologies such as real-time X-ray imaging or automated ultrasonic testing can assist in identifying porosity early in the welding procedure, enabling immediate rehabilitative activities. In general, incorporating these advanced remedies can substantially boost porosity control and boost the general quality of bonded components.
Final Thought
Finally, understanding the scientific research behind porosity in welding is necessary for welders and producers to produce top quality welds. By determining the elements affecting porosity development and implementing techniques to lessen it, welders can enhance the overall weld top quality. Advanced options for porosity control can additionally enhance the welding procedure and make sure a solid and trusted weld. It is vital for welders to continuously enlighten themselves on porosity and apply ideal practices to accomplish ideal results.